What’s the Winning Strategy for This Pharmaceutical Packaging Material Enterprise?
Changes in the policies of the pharmaceutical industry, the adjustment of node links in the pharmaceutical supply chain, and the rise of new sales channels such as pharmaceutical e-commerce are changing the intelligent demand for logistics and warehousing in the pharmaceutical industry.
Achievements
- The transformation of the 7-layer dense high-rise warehouse of pharmaceutical packaging materials increases the storage capacity by 5.5 times
- The four-way shuttle replaces the manual forklift, and the comprehensive storage efficiency is increased by more than 3 times
- Customized combine pallet storage, reducing the cost of goods shipped with pallets
- Assist customers to sort out the warehousing operation process and launch the WMS system for the first time
- Configure storage equipment that matches the ambient temperature -10°C-40°C, and the equipment and system are running stably
Zikoo's Solution
- The building area of the vertical warehouse is 1895 ㎡, the height of the vertical warehouse is 17m, and there are 7 floors, 4100 cargo locations
- 4 sets of four-way shuttles, 4 sets of high-speed elevators, several conveyor , 1 set of WMS, WES, WCS, RCS software systems
- Cargo size 1300*1200*2000mm (including pallet)
Challenges
- The horizontal warehouse of pharmaceutical packaging materials is transformed into a three-dimensional high warehouse to expand the storage capacity of the warehouse
- Realize warehousing automation, automatic inventory checking ,inbound &outbound
- Warehouse ambient temperature -10°C-40°C, stable operation of equipment and systems
- The goods are shipped on pallets and stored in the form of combine pallets
Project Background
Changes in the policies of the pharmaceutical industry, the adjustment of node links in the pharmaceutical supply chain, and the rise of new sales channels such as pharmaceutical e-commerce are changing the intelligent demand for logistics and warehousing in the pharmaceutical industry. Management regulations such as GMP and GSP run through the entire production and operation process of the pharmaceutical industry, and warehouse information management has become an important means for the pharmaceutical industry to efficiently implement regulations and promote compliant production and sales.
Industry Case Study
With the continuous development of national support policies and medical reforms, China’s pharmaceutical industry and its upstream and downstream supply chains have maintained steady growth. The increased investment in new drug research and development by pharmaceutical companies, along with the emergence of new drug forms, varieties, and specifications, has further driven the demand for pharmaceutical packaging materials. Consequently, the accompanying logistics supply chain is undergoing a transformation. The application of the new generation of intelligent logistics technologies, exemplified by intelligent four-way shuttle systems, has achieved a digital upgrade in internal logistics and warehousing, significantly enhancing storage efficiency and reducing labor costs.
Recently, Zikoo Robotics collaborated with Cangzhou Sihai Thermic Glass Co., Ltd., a well-known domestic producer of pharmaceutical glass bottles, to create an intelligent four-way vehicle high-density storage project. This initiative aims to establish a new benchmark in the pharmaceutical industry for intelligent warehousing by achieving intense storage and upgrading operations to automated and intelligent systems.
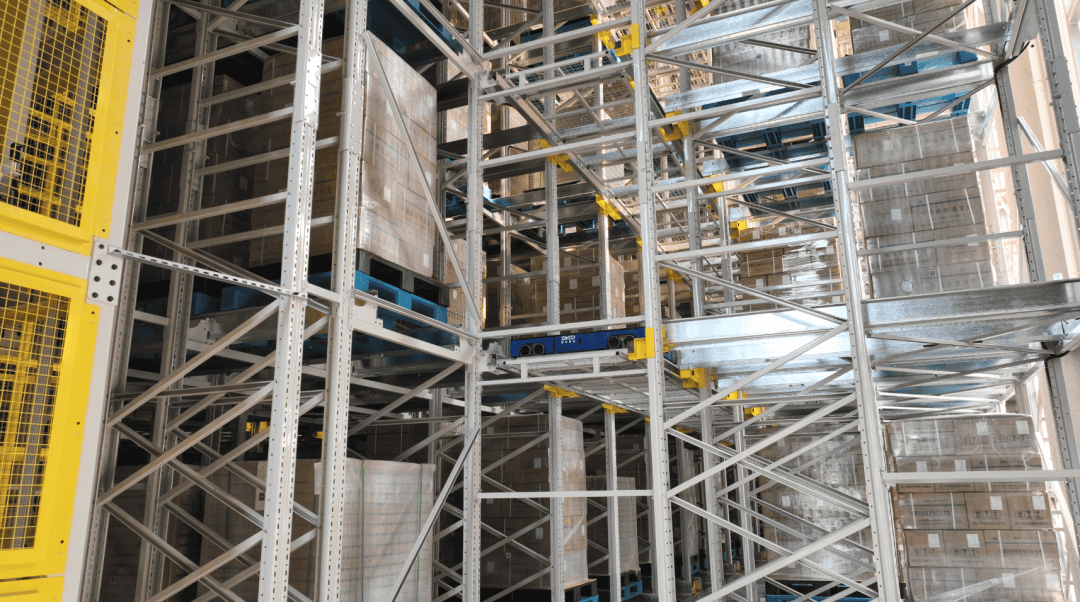
Project Pain Points
Large Warehouse Space and Storage Position Requirements
The warehouse spans 1900 square meters with a significant demand for storage positions, and the flat storage method urgently needed upgrading.
Inconsistent Pallet Sizes
Low Storage Density and Inefficient Manual Operations
Difficulty in Obtaining Information for Single Boxes and Whole Pallets
Ineffective Control and Management of Storage Positions and Inventory
In response to these challenges, Zikoo Robotics, leveraging its experience from over 400 successful projects, provided a range of hardware including four-way pallet vehicles, high-speed elevators, and conveyor lines. Additionally, they developed a custom intelligent warehousing software suite (IWMS, IWCS, RMS) to facilitate unmanned, intelligent, and flexible operations throughout the entire process of “storage-retrieval-outbound” for raw and auxiliary materials.
The project features two inbound and outbound gates directly connected to warehouse doors, compatible with manual forklifts and AGVs. After goods pass through shape detection and scanning for information verification, a storage request is sent to the IWMS system. The goods are then transported via conveyor line to the elevators and lifted to the designated storage level, where four-way vehicles transfer them to their assigned positions, and the backend system updates inventory information in real-time.
For outbound operations, based on orders or plans, IWMS issues instructions, and the IWCS system dispatches four-way shuttles to retrieve goods, which are then transported to the ground level and conveyed to the exit for whole-pallet outbound. Any empty pallets are transported to a pallet dismantling machine for temporary storage.
High-Density Storage with a 5.5 Times Increase in Capacity
The automated high-density warehouse consists of seven levels, reaching a height of 20 meters and offering 4100 storage positions. This maximizes space utilization, increasing storage capacity by 5.5 times. The multi-depth storage design accommodates a variety of goods, and the flexible operation of four-way pallet vehicles across multiple levels significantly improves inbound and outbound efficiency.
Highly Efficient Automated Operations with an 80% Increase in Efficiency
Equipped with four four-way pallet shuttles and four elevators, the intelligent logistics system communicates with IWMS and IWCS software to enable multi-vehicle dispatch and flexible operation deployment. The integration of warehouse gates ensures efficient whole-pallet handling, achieving an inbound and outbound efficiency of 55 pallets per hour. Compared to traditional methods, this represents an 80% increase in operational efficiency within the same area, significantly reducing labor costs.
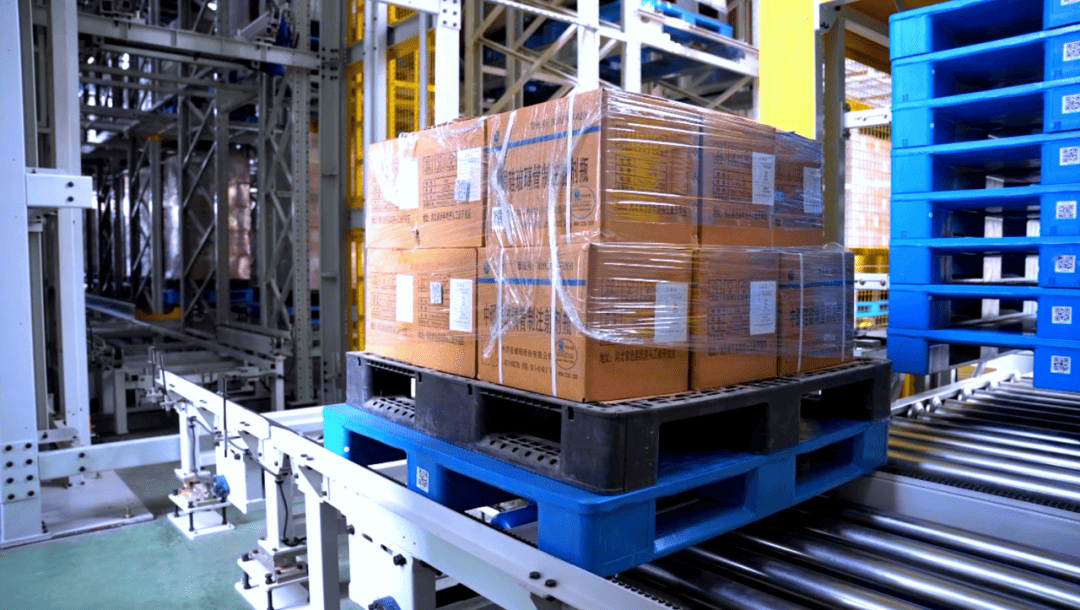
High-Precision Identification with 100% Accuracy
Tailoring to the client’s storage requirements, an automatic weighing device for inbound goods was installed. The weighing system checks the number of boxes and prohibits storage if the count is incorrect, triggering an alarm. The system also automatically records weight data, and any overweight alerts are promptly indicated. This 100% accurate identification greatly enhances material management efficiency.
Highly Adaptable to Various Pallet Specifications
To accommodate the diverse sizes of incoming materials and pallets, the project utilizes a parent-child pallet storage method. The front-end conveyance equipment works in tandem with a pallet dismantling machine. When goods need to be stored, the machine automatically separates the parent pallet, and workers place the incoming materials onto it. This method ensures uniformity of material specifications, allowing conveyance, lifting equipment, shelves, and four-way shuttles to accommodate a variety of pallet sizes, enabling flexible operations.
Related Products
Contact Us
Zikoo Robotics
Contact ZIKOO Robotics automation experts and learn how we can increase your operating efficiency and increase storage density.
Address
4F, Building 4, No. 170-1 Software Avenue, Yuhuatai District, Nanjing, China
Phone
(+86)-13851470374