As the logistics industry increasingly embraces automation, solutions like the four-way shuttle system are at the forefront of transforming warehouse operations. These systems are essential in intelligent warehousing, providing faster processes, higher storage density, and reduced costs. In this article, we’ll explore how to quickly deploy a shuttle warehouse system, ensuring seamless integration into your operations.
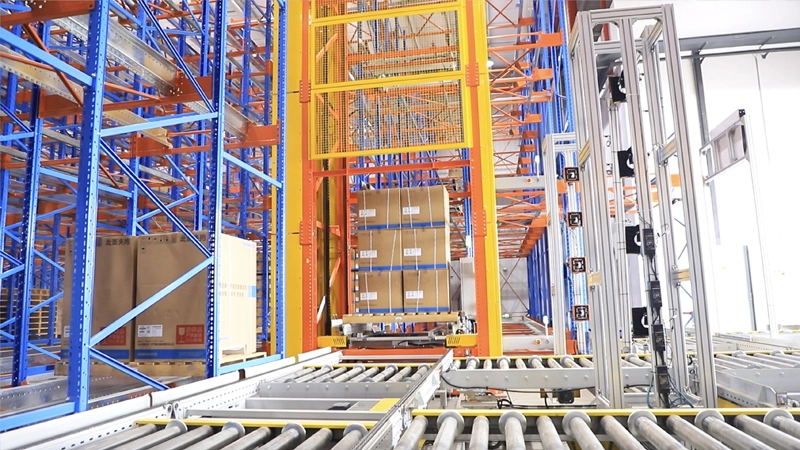
1. Assess Your Warehouse Needs
The foundation of any successful automated storage solution begins with understanding your specific warehouse requirements. Key aspects to evaluate include:
- Storage capacity: What is the maximum amount of goods you need to store?
- Goods types: Are you storing pallets, cartons, or irregular-shaped items?
- Turnover rates: What is the flow rate of goods in and out of your warehouse?
- Environmental conditions: Consider temperature, humidity, and other factors that could impact storage.
By evaluating these factors, you can ensure that your automated pallet shuttle system is tailored to your unique needs. This will enable optimal performance right from the start.
2. Design Your Four-Way Shuttle System
A well-thought-out system design is crucial for optimizing your warehouse’s efficiency. Key elements of the design process include:
- Rack layout: Maximize available vertical and horizontal space to increase storage density.
- Path planning: Minimize travel time for the four-way shuttle by ensuring efficient routes.
- Integration with other automation: Combine your shuttles with lifts, conveyors, and AGVs (Automated Guided Vehicles) to create a fully integrated system.
- Software synchronization: Ensure that WMS (Warehouse Management System) and WCS (Warehouse Control System) are integrated to track inventory and manage operations smoothly.
This comprehensive design approach will ensure that all systems work in harmony, providing maximum efficiency.
3. Efficient Installation and Testing
Once your design is finalized, it’s time to move to the implementation phase. The key steps include:
- System installation: Set up racks, tracks, and the shuttle warehouse system.
- Calibration and testing: Test the shuttle system’s functionality with the lifts, conveyors, and software to ensure everything works seamlessly.
- Trial runs: Conduct trial runs to simulate actual operations, identifying potential issues that need to be addressed before going live.
Collaborating with experienced partners during this phase can accelerate deployment and reduce the risk of mistakes.
4. Optimize and Maintain Your System
Once the system is operational, it’s important to optimize performance for ongoing efficiency:
- Use real-time data analytics to fine-tune shuttle operations and improve workflow efficiency.
- Schedule regular maintenance for the shuttles, lifts, and software systems to prevent downtime.
Why Choose a Four-Way Shuttle for Intelligent Warehousing?
The four-way shuttle system offers several benefits over traditional storage methods:
- Flexibility: Shuttles can move in multiple directions, making it easier to access goods quickly and efficiently.
- Scalability: As your storage needs grow, the system can be expanded without major overhauls.
- Increased throughput: Handle high volumes of goods with ease, improving operational efficiency and throughput.
Accelerate Your Warehouse Transformation
At Zikoo Robotics, we specialize in designing and deploying automated pallet shuttle systems for businesses worldwide. Our intelligent warehousing solutions help you achieve higher efficiency and drive sustainable growth.
Keywords:
shuttle warehouse