Auto Parts Manufacturer achieving 70% Storage Increase and 80% Efficiency Boost
Leading Automotive Manufacturer in Suzhou Partners with Zikoo Robotics to Implement Comprehensive Smart Warehousing Solution, Boosting Storage Capacity by 70% and Operational Efficiency by 80%
Achievements
- Built an intensive storage system, with four-way shuttles capable of flexibly maneuvering around columns.
- Equipped with two pallet sizes, managing a variety of materials through WMS, WCS, and RCS.
- Constructed an aerial corridor, using conveyor lines for interconnected operations between the warehouse and the workshop, creating an integrated smart production line.
- Coordinated multiple devices for efficient inventory management, achieving an impressive rate of up to 123 pallets/hour.
Zikoo's Solution
- Constructed a high-density storage system with a total area of 2973 sqm, a clear height of 11m, and a five-level storage system with 6350 storage positions, featuring 4 inbound and outbound ports.
- Equipped with 7 four-way shuttles, 6 elevators, several conveyor lines, and a complete set of WMS, WES, WCS, and RCS software systems.
Challenges
- Warehouse with many columns, including diagonal braces and cross-bracing, leading to significant space constraints.
- Mixed storage of raw materials and finished products, with varying dimensions.
- Production line and warehouse located in separate buildings, necessitating cross-area connection.
- Low warehouse throughput efficiency and high labor costs.
Project Background
With rapid technological innovation and changes in consumer demand patterns, the manufacturing market is becoming increasingly competitive. The need for product upgrades and the optimization of supply chains are accelerating. Models like Vendor Managed Inventory (VMI) warehouses are widely applied to address challenges such as limited production space, high inventory costs, and low shipping efficiency in manufacturing enterprises, hastening their transition towards smart production and logistics.
How to Achieve 24-Hour Automated Warehousing
In the forefront of the automotive manufacturing industry, a leading automotive parts production company has partnered with Zikoo Robotics to implement a comprehensive intelligent warehousing solution. This collaboration has led to the creation of a multi-tiered storage system for auto parts. Through the automated coordination of multiple robots across different floors, the company has achieved seamless transportation from production to storage across factory areas, enhancing the entire process with digitization, automation, and intelligence. This transformation has resulted in a 70% increase in storage capacity and an 80% improvement in operational efficiency, significantly elevating the level of warehouse management.
With the growth of the internet economy, the automotive parts industry has been expanding rapidly. Automotive parts are characterized by their diverse types, varying specifications, and short product life cycles. Traditional warehousing methods have reached a bottleneck, with low space utilization and a lack of intelligent systems leading to inefficiencies in storage logistics. These challenges, coupled with high operational costs, fail to meet current demands. Thus, automotive parts manufacturers are urgently seeking new breakthroughs to cope with the industry’s need for flexibility, intelligence, and highly integrated smart manufacturing systems to reduce costs and improve efficiency.

Solution
Zikoo Robotics constructed a five-level automated storage system with four-way shuttle cars, spanning an area of 2973 square meters. The system uses pallet storage and is equipped with specially designed multi-depth shelving for the four-way shuttles. It features seven intelligent four-way shuttle cars, six high-speed elevators, and flexible conveyor line equipment, complemented by Warehouse Management System (WMS) and Warehouse Control System (WCS) software.
The intelligent scheduling of the four-way shuttle cars, based on order workload and operational conditions, facilitates multi-level and multi-area operation. This system not only interfaces seamlessly with production lines for 24-hour continuous operation but also allows for detailed and digitized control of materials.
Project Highlights
- Efficient Storage with Four-Way Shuttle Cars: The automated storage system increases space utilization by 70% compared to traditional warehouses. The flexibility of the shuttle cars in operating across multiple shelving levels significantly boosts storage and retrieval efficiency, overcoming the limitations of traditional warehouses that have a single access aisle.
- Continuous 24-Hour Operation Across Factory Areas: A corridor set within the warehouse, along with the integration of conveyor lines and elevators, seamlessly connects production lines with the storage system, allowing for continuous automated transportation and 24-hour operation.
- Compatibility with Various Pallet Sizes: The automotive industry requires different pallet sizes due to varying models and brands. This project employs a unique design allowing the conveyor elevators, shelving, and shuttle cars to accommodate various pallet specifications, enabling flexible operations.
- Intelligent Operation, Reducing Labor Costs: The implementation of WMS and WCS software systems, integrated with intelligent logistics equipment, allows for fully automated and unmanned operations. This not only ensures intelligent operation but also significantly reduces labor costs.
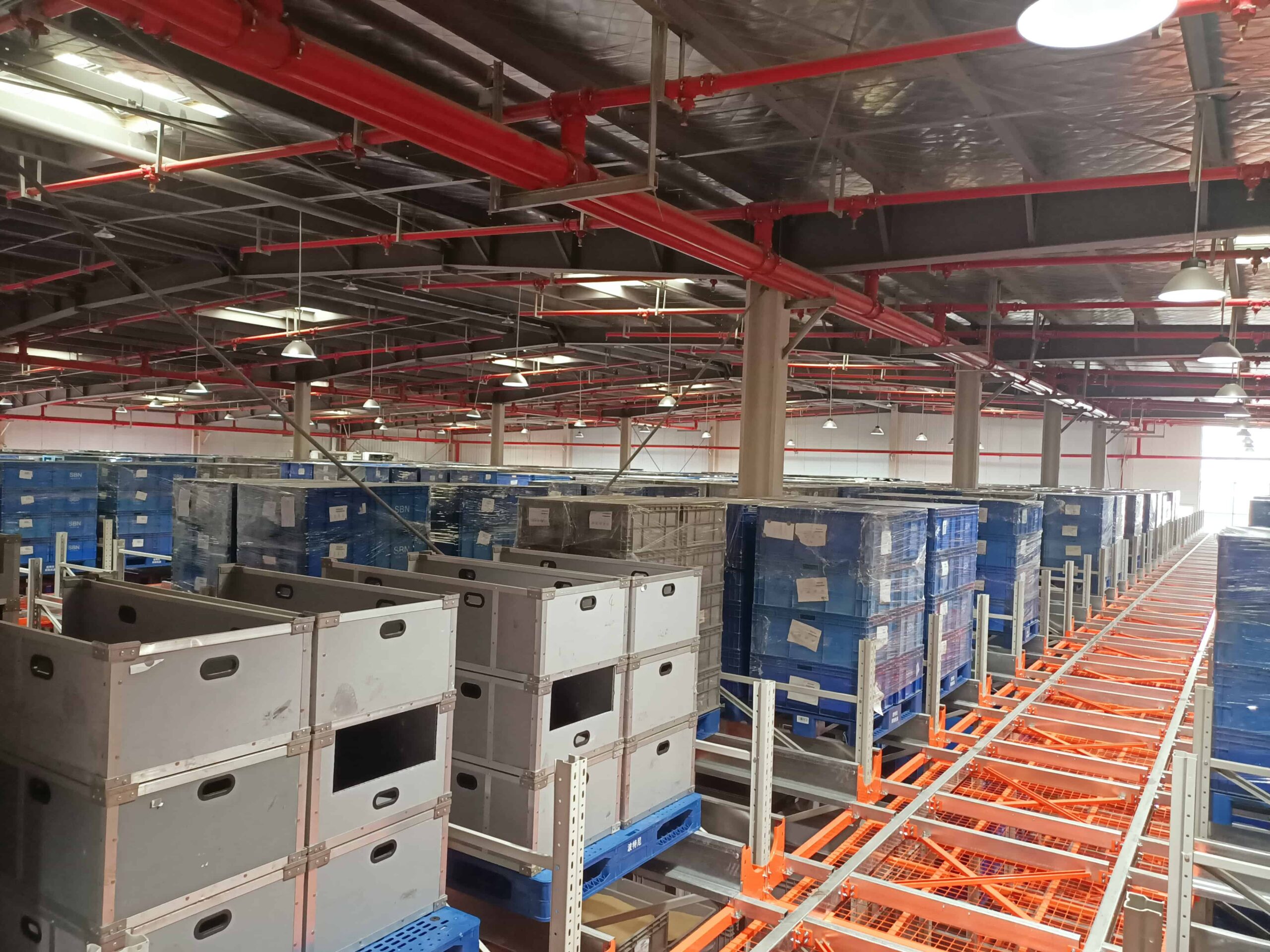
Project Outcomes
- Increased Space Utilization: The five-level four-way shuttle car warehouse with multi-depth shelving has increased storage capacity by 70%.
- Improved Operational Efficiency: The deployment of seven intelligent four-way shuttle cars and other automated logistics equipment enables multi-car dispatching and multi-level operation, enhancing efficiency by 80% overall.
- Reduced Labor Costs: The use of automated logistics equipment like four-way shuttle cars in the warehouse reduces the need for manpower, thereby cutting labor costs and minimizing errors caused by manual operations.
- Faster Turnover of Materials: The seamless integration of production lines with the automated storage system enables continuous 24-hour operation, accelerating the turnover rate of materials.
Related Products
Contact Us
Zikoo Robotics
Contact ZIKOO Robotics automation experts and learn how we can increase your operating efficiency and increase storage density.
Address
4F, Building 4, No. 170-1 Software Avenue, Yuhuatai District, Nanjing, China
Phone
(+86)-13851470374