Wandian No.1″ – What Makes It Stand Out as an Intelligent Warehouse?
When discussing contemporary intelligent warehouses, the first that comes to mind is JD’s “Asia No.1” warehouse. Its dazzling promotional videos showcase various AGVs efficiently operating in their designated roles. Next in line is Amazon’s warehouse, where the Kiva robots significantly contribute to the development of intelligent warehouse equipment.
Achievements
- Build 3 kinds of warehouses + 1 storage system to realize “goods-to-person” intelligent storage and picking
- Realize intelligent matching and error reporting with the help of Internet of Things technologies such as face recognition and intelligent security
- Equipped with an intelligent software system PC-side smart large screen + handheld terminal APP to realize the whole process information management
Zikoo's Solution
- The total area of the warehouse is 8142㎡, with a net height of 7.5m. The overall planning includes a four-way shuttle car three-dimensional warehouse, a beam-type shelf AGV warehouse, a piggyback AGV picking warehouse, and an unattended warehouse. It is also equipped with a central control room, a service hall, and a meeting room At the same time, information facilities such as face recognition, smart security, WMS system, and handheld operation APP are deployed.
- Among them, the four-way three-dimensional warehouse covers an area of 1260 square meters, with 3 layers of shelves, 1272 cargo spaces, 6 four-way shuttle cars, 2 hoists, and 1 set of WMS, WES, WCS, and RCS software systems.
Challenges
- The materials in the warehouse are complex and diverse, and the weight of a single pallet is as high as 1.5T
- The response speed of material receiving is low and the security is high
- Low warehouse management efficiency and low degree of informatization
- Realize multi-type warehouse scenarios, combined with face recognition, smart security and other informatization supporting facilities
Project Background
With the sharp increase in the demand for power supplies brought about by the transformation and upgrading of the power grid, the storage period of power enterprise warehouses is shortened, the turnover rate is accelerated, and the frequency of in and out of warehouses is increasing. Traditional warehouses can no longer meet the needs of development and construction. Especially in the face of disaster preparedness and emergency response to power emergencies, the efficient storage and storage of power materials is the key to ensuring power recovery, and smart supply chain reform is urgently needed.
A Real-World Insight into “ Wandian No.1 ”
When discussing contemporary intelligent warehouses, the first that comes to mind is JD’s “Asia No.1” warehouse. Its dazzling promotional videos showcase various AGVs efficiently operating in their designated roles. Next in line is Amazon’s warehouse, where the Kiva robots significantly contribute to the development of intelligent warehouse equipment.
However, there seems to be a common misconception: the more automated storage equipment and the fewer operational staff in an advanced intelligent warehouse, the better. Information technology is just a foundation, while concepts like AI, big data, IoT, and AIoT, as well as substantial investments often running into millions or even billions, are seen as markers of advancement. Does this imply that the costlier the warehouse, the more advanced it is?
Recently, a warehouse colloquially known as “Wandian No.1” was officially completed. Boasting the latest equipment, technology, and management methods, my visit there was unexpectedly different. The futuristic and technological feel often portrayed in intelligent warehouse videos was absent. Instead, I found a sense of simplicity, with a few busy storage management staff preparing for the warehouse’s upcoming operation.
Optimizing Space Utilization
From an architectural perspective, the warehouse measures approximately 134.8 meters in length and 60.4 meters in width, covering an area of 8,142 square meters. It’s a single-story steel structure with a usable height of about 7 meters. On the west side, there is a steel structure platform of about 1,300 square meters, and on the east side, there’s a two-story office building primarily used for tools storage.
The warehouse is strategically designed with various functional areas including a four-way shuttle storage area, an unmanned forklift storage area, an AGV picking area, an unmanned warehouse area, a functional area, an indoor flat storage area, and a platform flat storage area.
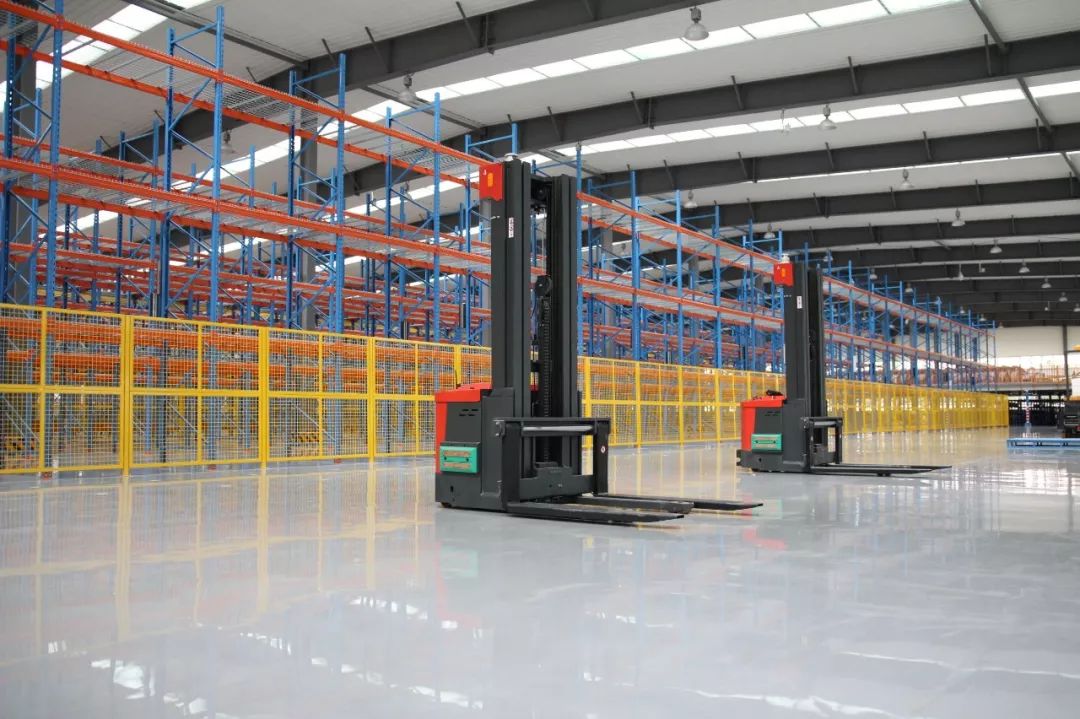
The Unmanned Forklift and Shuttle Car System
The four-way shuttle storage system consists of 2 conveyor lines, 1 pallet stacking machine, 2 elevators, 3 four-way shuttles, and high-rise pallet racks covering 1,650 square meters. It uses 1600*1200*150mm steel pallets for storing materials smaller than 1600*1200*1600mm, with racks on 3 floors housing 1005 pallet positions. The system’s total operational capacity reaches 40 pallets/hour.
The unmanned forklift storage area, designated for items like cable branch boxes, switch cabinets, and transformers, has an effective storage area of about 1370 square meters. It primarily features standard heavy-duty racks using 2000*1400*150mm steel pallets, with 4 levels and 456 pallet positions, each bearing a load of 2 tons. Two reach-type unmanned forklifts are equipped, with a main operating channel of 4 meters, designed in a circular layout.
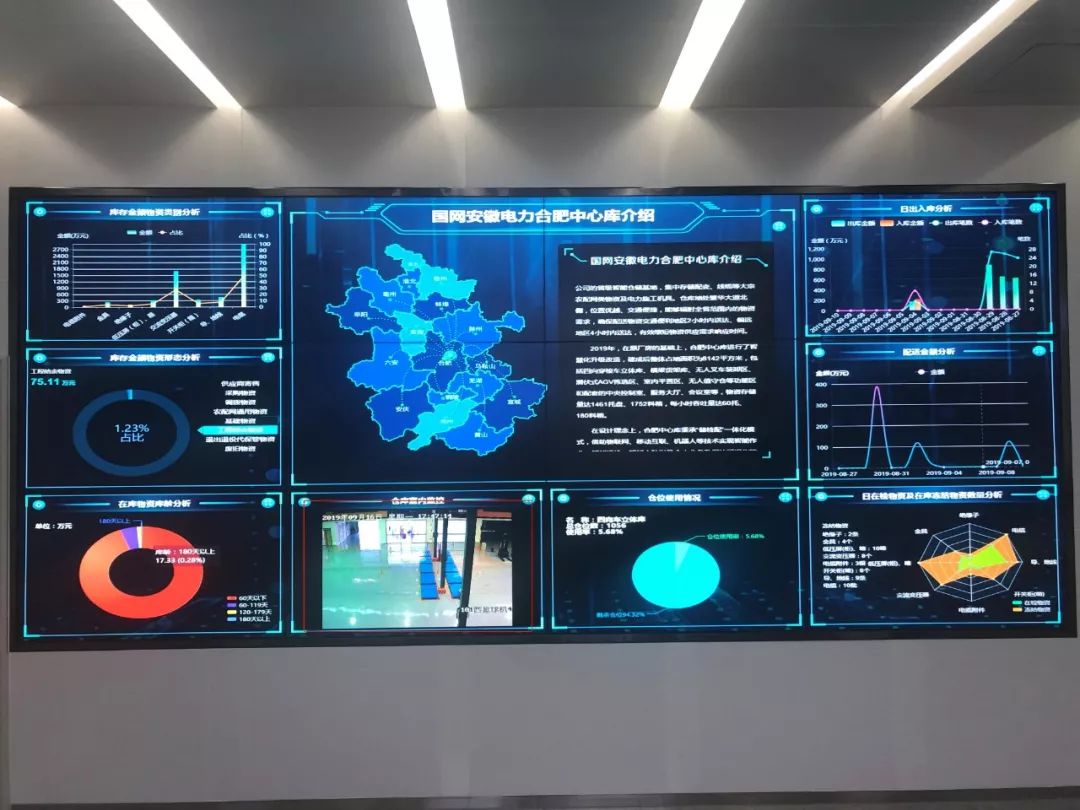
Revolutionizing Warehouse Management
The AGV “goods-to-person” picking system is tailored for small items like fittings, cable terminals, and wires. Backpack-type AGVs are used for transportation, with storage in 3-level picking racks and bins. This area is equipped with 2 fully automatic guide shuttles and 110 sets of picking racks, each with a load capacity of no less than 500KG.
The unmanned warehouse area is one of the highlights of “Wandian No.1,” innovatively introducing the concept of an “unmanned warehouse.” This area mainly stores a variety of items used in substation operation and emergency repair, which are lightweight, diversely shaped, unpackaged, and frequently used. It employs an “automated vertical storage cabinet system,” combining weight-based SKU identification and counting modules, facial recognition access control, vertical storage systems, and warehouse management systems. With IoT and machine vision technologies, this truly achieves “pick-and-go.” Upon facial recognition entry, the system matches faces with picking lists. Users are guided by lasers to collect items and verify picking information. If the wrong item is picked, the system automatically alarms, eliminating the need for supervision and paper documentation, thus significantly saving labor and improving the efficiency and management level of emergency material usage.
In terms of information technology, “Wandian No.1” showcases several innovations. Data analysis leverages the intelligent central control platform for data mining, presenting business data like inventory value, shelf life, inbound/outbound, transfer, and distribution in a visually engaging format. In warehouse management, digital twin technology is used for 3D mapping of the four-way shuttle storage, showing real-time equipment and inventory status. For intelligent security, a safety helmet positioning system using UWB positioning technology can track personnel status in real time.
Related Products
Contact Us
Zikoo Robotics
Contact ZIKOO Robotics automation experts and learn how we can increase your operating efficiency and increase storage density.
Address
4F, Building 4, No. 170-1 Software Avenue, Yuhuatai District, Nanjing, China
Phone
(+86)-13851470374